Introduction
The integrity and longevity of piping systems within water and wastewater treatment plants are paramount. A common oversight in these projects is the inadequate specification of stainless steel, particularly the failure to mandate low-carbon grades. This oversight can lead to severe corrosion issues, compromising system reliability and safety.
Many piping specialists and fabricators underestimate the critical difference between standard stainless steel (SS304/316) and its low-carbon counterparts (SS304L/316L). Specifying “SS304/SS304L” or “SS316/316L” in piping class or vessel specifications creates ambiguity, potentially allowing the choice of standard grades. This ambiguity poses a significant risk to the project’s long-term performance. Piping class and vessel specifications must explicitly state “SS304L” or “SS316L” to ensure the appropriate material is utilized.
Why Low Carbon Stainless Steel is Essential
The primary advantage of low-carbon stainless steel lies in its enhanced corrosion resistance, particularly after welding.
Sensitization and Intergranular Corrosion of Stainless Steel
Welding standard stainless steel can make it susceptible to corrosion. The intense heat of welding causes chromium carbides to form at the grain boundaries within the heat-affected zone. This “sensitization” depletes the surrounding areas of chromium, which is essential for the steel’s protective layer. Consequently, the material becomes prone to intergranular corrosion.
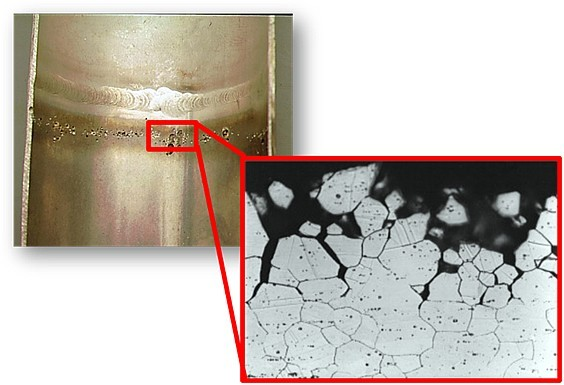
The Role of Low Carbon SS
Low-carbon stainless steel, such as SS304L and SS316L, minimizes the formation of chromium carbides. This significantly reduces the risk of sensitization and subsequent intergranular corrosion, especially in welded applications.
In essence, using low-carbon versions of SS304 and 316 ensures that the stainless steel retains its desired corrosion-resistant properties, especially in applications involving welding.
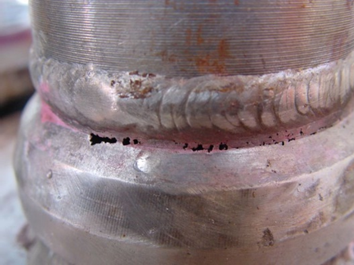
Conclusion:
To ensure the long-term integrity of welded piping systems in water and wastewater treatment plants, the use of low-carbon stainless steel (SS304L/316L) is imperative. As a practical rule:
“Always use the ‘L’ grades if there is any chance that the system will be welded.”
Verification of Material Composition:
It is important to know that there is no visual way to differentiate between standard and low-carbon grades.
It is crucial to verify that the fabricator utilizes the specified low-carbon stainless steel.
The fundamental difference between both grades is their carbon content, and its verification can be achieved through:
- Material Test Reports/Certifications: Examination of material test reports or certifications accompanying the stainless steel.
- Chemical Analysis: Laboratory chemical analysis can accurately determine the carbon content. While definitive, this method may not always be practical for routine verification.
By adhering to these guidelines, project engineers and managers can mitigate the risk of corrosion and ensure the reliable operation of critical piping systems.
References:
- Special Steel Industry of North America. Visit: Intergranular Attack of Austenitic Corrosion of SS
- AMARINE Blog: Stainless Steel Welding Notes
- The Fabricator.com: What makes stainless steel stainless?
- Photo 1: Courtesy of Blog MatIntegrity. Visit: MatIntegrity
- Photo 2: Courtesy of Clifford Mathews Wilkinson Coutts Engineering Training Ltd